Impresoras 3D: una revolución en la fabricación aeronáutica.
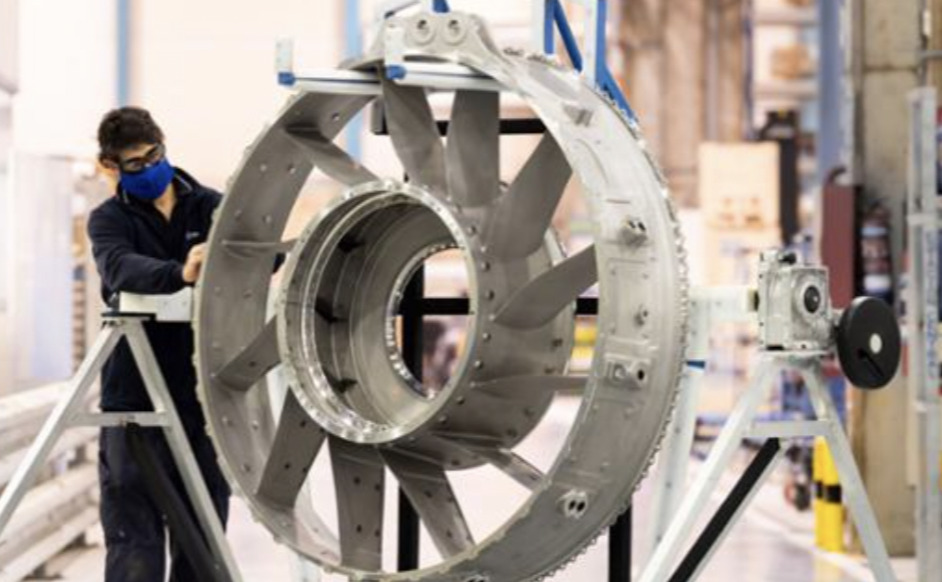
ITP Aero ha marcado un antes y un después en la industria aeroespacial al obtener la certificación para una pieza estructural de motor fabricada mediante tecnología aditiva. Este avance supone un paso significativo en la fabricación de componentes aeronáuticos, gracias a la utilización de impresoras 3D.
Aunque el sueño de volar en aviones completamente impresos en 3D aún parece lejano, este desarrollo demuestra el potencial de la fabricación aditiva para transformar la ingeniería aeronáutica. Erlantz Cristóbal, director ejecutivo de Ingeniería y Tecnología en ITP Aero, lo resume así: “Hemos logrado certificar nuestras propias normas y procesos de fabricación aditiva para producir componentes de motores de aviación diseñados para soportar altas temperaturas”.
Pequeñas piezas, grandes avances
El hito alcanzado por ITP Aero se centra en los álabes de la estructura trasera del motor TP400, piezas clave en el flujo de aire y generación de energía de los motores. Aunque no superan los 20 centímetros de tamaño ni el medio kilo de peso, son capaces de resistir temperaturas de hasta 700 grados. Estas cuchillas han sido certificadas por la Agencia de Seguridad Aérea de la Unión Europea (EASA) y la Agencia Española de Seguridad Aérea (AESA) para su uso en motores de turbina y reacción.
El camino hacia la certificación no fue sencillo. Según Cristóbal, tuvieron que demostrar que su proceso es robusto y consistente, desde la cualificación de equipos hasta la validación de materiales y controles de calidad.
María Cañas, responsable de Tecnología Aditiva en ITP Aero, destaca la importancia de este logro: “Esta es la primera pieza estructural fabricada con tecnología aditiva que obtiene certificación. Hasta ahora, este componente se producía mediante métodos convencionales como la forja y la fundición. Ahora hemos abierto la puerta a desarrollar piezas más complejas con este método”.
La magia de la fabricación aditiva
El proceso utilizado es la fusión selectiva por láser, una técnica que permite crear piezas capa por capa con gran precisión. Un modelo 3D se divide digitalmente en capas de apenas 60 micras, el grosor de un cabello humano. Luego, un láser funde polvo de superaleación de níquel para formar el componente final. Este método, que utiliza 2.500 capas para fabricar cada pieza, es altamente eficiente en términos de consumo de materiales y energía.
“A diferencia de los métodos tradicionales, casi todo el material utilizado se convierte en parte de la pieza final”, explica Cañas. Esto no solo reduce el desperdicio, sino también el impacto ambiental. Además, las piezas resultantes son más ligeras y contienen menos componentes, lo que mejora la eficiencia del avión y reduce sus costos operativos.
La tecnología aditiva también permite diseñar componentes más complejos en menos tiempo, optimizando recursos y agilizando la cadena de suministro. Según Cañas, la simulación digital previa asegura una fabricación precisa, reduciendo errores y acelerando los tiempos de desarrollo.
Un nuevo centro para la innovación
Para seguir avanzando en esta tecnología, ITP Aero está construyendo un centro de investigación y desarrollo en Zamudio, Bizkaia, llamado Admire. Con una inversión de 23 millones de euros, este centro albergará tecnologías de fabricación avanzada, incluida la impresión 3D, y contará con un equipo de 120 ingenieros y especialistas.
Según Cristóbal, el objetivo es atender las demandas cambiantes del mercado y alinearse con los objetivos de sostenibilidad de la empresa: “Si logramos reducir el peso de los aviones, podríamos extender la autonomía de los vuelos y mejorar su eficiencia”.
Cifras récord en ITP Aero
El éxito en fabricación aditiva coincide con un momento de crecimiento para ITP Aero. En 2023, la empresa registró ingresos récord de 1.305 millones de euros, un 25% más que el año anterior. Este aumento se debe al impulso del sector comercial tras la pandemia y a la expansión en el ámbito de la defensa.
Además, la compañía incrementó su plantilla con 500 nuevas contrataciones, superando los 5.000 empleados, y aumentó su inversión en I+D hasta los 66 millones de euros.
El futuro de la aviación aditiva
El avance logrado con la fabricación aditiva es solo el comienzo. ITP Aero planea desarrollar más componentes utilizando esta tecnología, lo que podría revolucionar la industria aeronáutica. Como concluye Cristóbal: “Estamos pensando en el futuro. Si podemos fabricar aviones más ligeros, podemos soñar con vuelos más largos y sostenibles”.